Maximizing Efficiency and Precision in Your Woodworking Projects
Learn tips and techniques to maximize efficiency and precision in your woodworking projects. Transform your craftsmanship skills today.
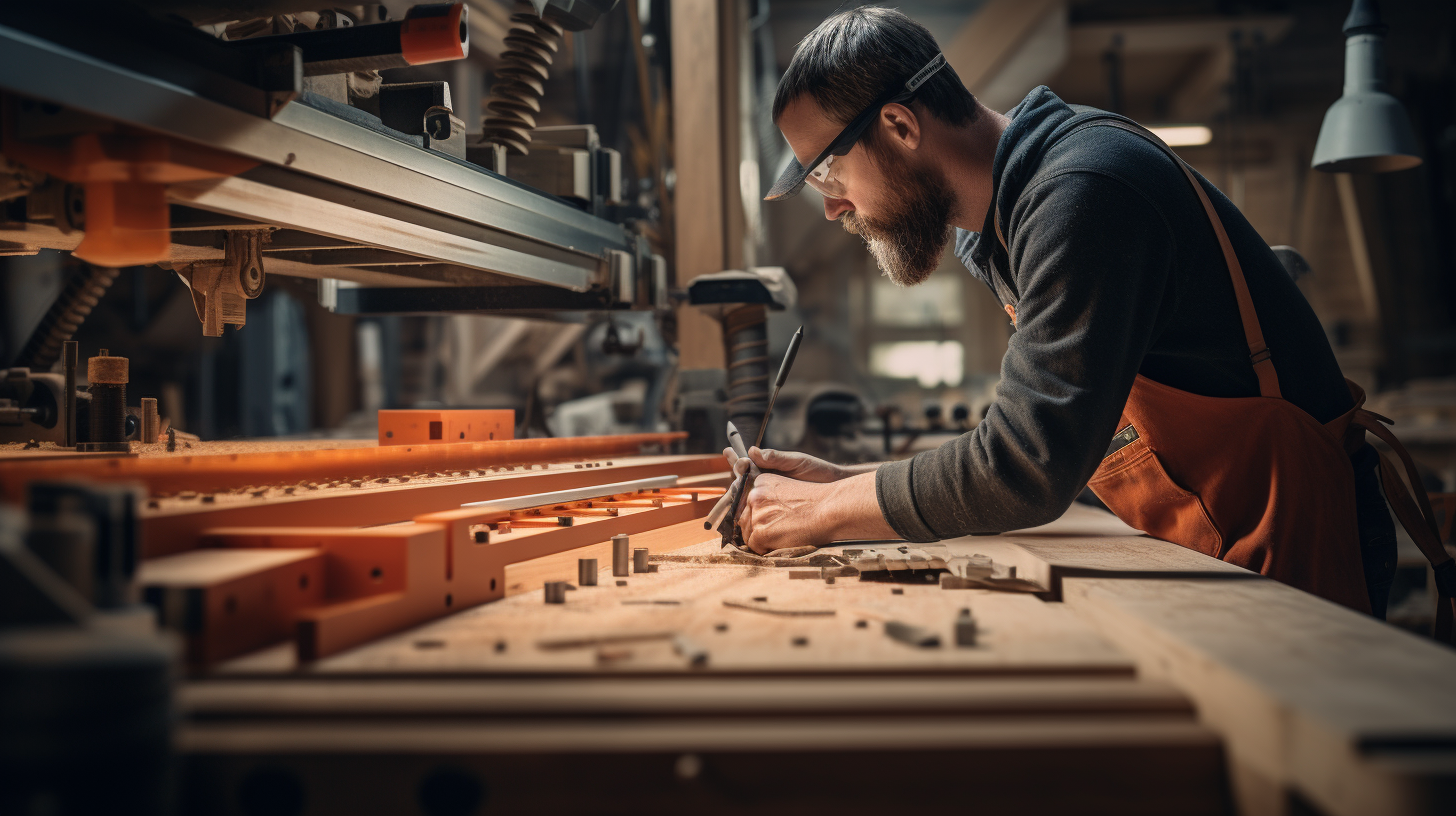
Welcome to the world of woodworking! Whether you're a beginner or an experienced DIY enthusiast, woodworking can be a fulfilling and rewarding hobby. There's nothing quite like the satisfaction of creating something beautiful and functional with your own two hands.
In this article, we'll explore the essential techniques and tips to help you maximize efficiency and precision in your woodworking projects. From setting up your woodworking workshop to selecting the right wood and mastering cutting and shaping methods, we've got you covered.
So, grab your safety goggles and let's dive in!
Setting Up Your Woodworking Workshop
Whether you're a seasoned woodworker or just starting out, having a well-equipped and organized workshop is essential for maximizing efficiency and precision in your woodworking projects. A well-planned workshop not only makes your work easier but also ensures safety and a smooth workflow. In this section, we'll discuss some key factors to consider when setting up your woodworking workshop.
Choosing the Right Space
Before diving into the tools and equipment, it's important to find the right space for your workshop. Here are a few things to consider when selecting a suitable area:
- Size: Ensure that you have enough space to comfortably accommodate your tools, workbenches, and storage units. A cluttered and cramped workshop can hinder your productivity and make it difficult to work on larger projects.
- Ventilation: Woodworking involves working with various materials and chemicals, some of which can produce harmful fumes. Adequate ventilation is crucial to maintain a healthy working environment. Consider installing windows, exhaust fans, or even a workshop air filtration system.
- Accessibility: Opt for a space that is easily accessible, both for you and for moving materials in and out of the workshop. If possible, choose a location close to the main entrance of your home or garage.
- Lighting: Good lighting is essential for accurate and precise work. Natural light is ideal, so choose a space that has windows. Supplement the natural light with proper shop lighting fixtures.
Essential Tools and Equipment
Now that you have a space for your workshop, let's talk about the essential tools and equipment every woodworker should have. While the specific tools you need may vary depending on the type of woodworking you do, here are some basics to get you started:
- Workbench: A sturdy workbench is the heart of any woodworking workshop. Make sure it's of the right height for comfortable use and has a solid, flat surface for accurate measurements and assembly.
- Power Tools: Invest in essential power tools like a table saw, miter saw, drill press, and router. These tools will help you make precise cuts, shape wood, and create various joinery techniques.
- Hand Tools: Don't overlook the value of good quality hand tools. A set of chisels, hand planes, saws, and measuring tools like a tape measure, square, and marking gauge are essential for fine woodworking and detail work.
- Safety Equipment: Safety should be a top priority in any workshop. Equip yourself with safety goggles, hearing protection, dust masks, and a fire extinguisher. Also, invest in a good-quality dust collection system to keep your workshop clean and free from harmful dust particles.
Safety Measures
Woodworking can be a potentially hazardous activity, so it's crucial to implement safety measures to protect yourself and others in the workshop. Here are some key safety guidelines to follow:
- Read the Manuals: Familiarize yourself with the instructions and safety guidelines provided by manufacturers for all your tools and equipment.
- Proper Handling of Tools: Learn how to handle each tool safely and correctly. Use tools with protective guards, and always keep your hands and fingers away from the cutting area.
- Eye and Ear Protection: Wear safety goggles to protect your eyes from flying wood chips and debris. Additionally, use ear protection when operating loud power tools to prevent hearing damage.
- Organize and Maintain: Keep your workshop clean and organized. A clutter-free workspace reduces the risk of accidents and allows for better workflow.
- Fire Safety: Have a fire extinguisher easily accessible in case of emergencies. Ensure that your workshop is equipped with proper electrical wiring and fire-resistant materials.
Setting up your woodworking workshop should be an exciting and rewarding process. By carefully selecting a suitable space, acquiring the right tools and equipment, and implementing safety measures, you'll create a workspace that not only enhances your woodworking experience but also ensures optimal efficiency and precision in your projects. So, roll up your sleeves, get creative, and let your woodworking journey begin!
"A well-organized and equipped workshop is like a playground for a woodworker—a place where creativity can thrive and woodworking dreams can come to life."
Selecting the Right Wood for Your Projects
When it comes to woodworking, one of the most important decisions you'll make is selecting the right wood for your projects. The choice of wood can greatly impact the appearance, durability, and overall quality of your finished pieces. With so many types of wood available, it can be overwhelming to know which one to choose. In this section, we will discuss some key considerations when selecting wood for your projects.
Understanding Different Types of Wood
Wood comes in a variety of species, each with its own unique characteristics and qualities. Some common types of wood used in woodworking include:
- Hardwoods: Hardwoods come from deciduous trees and are known for their durability. Examples include oak, walnut, cherry, and maple. Hardwoods are typically more expensive than softwoods but are well-suited for furniture making and other high-quality woodworking projects.
- Softwoods: Softwoods come from coniferous trees and are generally less expensive than hardwoods. Examples of softwoods include pine, cedar, and spruce. Softwoods are often used in construction and for making more utilitarian items.
- Exotic Woods: Exotic woods, such as mahogany, teak, and rosewood, come from trees found in tropical regions. These woods are sought after for their unique grain patterns, rich colors, and natural beauty. However, they can be more costly and may require special handling and finishing techniques.
Evaluating Wood Quality
Once you've narrowed down the type of wood you want to use, it's important to assess the quality of the wood before making a purchase. Here are some factors to consider:
- Moisture Content: Wood with high moisture content is prone to warping and can be challenging to work with. Look for wood that has been properly dried and has a moisture content of around 6-8%.
- Grain Pattern: The grain pattern of the wood can greatly impact its appearance. Some wood species have bold and distinct grain patterns, while others have a more subtle and uniform look. Consider the desired aesthetic of your project when selecting the wood grain.
- Knots and Defects: Knots and other defects can weaken the structure of the wood and make it more difficult to work with. Inspect the wood for any visible knots, cracks, or other imperfections that could affect its stability.
Sourcing Environmentally Friendly Wood
As a responsible woodworker, it's important to consider the environmental impact of your wood choices. Here are some tips for sourcing environmentally friendly wood:
- Look for Certified Wood: Look for wood that has been certified by organizations such as the Forest Stewardship Council (FSC) or the Sustainable Forestry Initiative (SFI). These certifications ensure that the wood has been harvested sustainably and responsibly.
- Reclaimed Wood: Consider using reclaimed wood, which is salvaged from old structures or furniture. Reclaimed wood not only reduces the demand for new lumber but also adds character and a story to your projects.
- Local and Domestic Wood: Choosing wood sourced locally or from domestic suppliers can help reduce the carbon footprint associated with shipping. Additionally, supporting local businesses and communities is always a good choice.
Remember, selecting the right wood is not only about aesthetics and project requirements but also about sustainability and responsible woodworking practices. Take your time to research and choose the best wood for your projects, and you'll be rewarded with beautiful, durable pieces that will stand the test of time.
Measuring and Marking Techniques
When it comes to woodworking, precision is key. To achieve accurate results in your woodworking projects, it is essential to master the art of measuring and marking. Whether you're working on a simple shelf or tackling a more intricate piece of furniture, using measuring tools accurately and efficiently is crucial. In this section, we will discuss some valuable measuring and marking techniques that will help you maximize efficiency and precision in your woodworking projects.
Using Measuring Tools Accurately
Measuring tools are the foundation of precise woodworking. Here are some tips for using them effectively:
- Tape Measure: Invest in a high-quality tape measure that is easy to read and provides accurate measurements. Hold the tape measure firmly while taking measurements to prevent any movement that could affect the accuracy of your measurements.
- Combination Square: A combination square is an invaluable tool for checking right angles and marking straight lines. Ensure that the square is aligned correctly by placing it against a straight edge and adjusting it if necessary.
- Calipers: Calipers are ideal for measuring small and precise dimensions. Whether you're measuring the thickness of wood or the diameter of a hole, calipers can provide the accuracy you need. Make sure to zero the calipers before taking measurements.
Marking Guidelines and Reference Points
Once you have taken accurate measurements, the next step is to mark guidelines and reference points on your wood. These markings serve as a guide for cutting, drilling, and shaping. Here are some techniques to help you achieve precise markings:
- Pencils and Marking Knives: Use a sharp pencil or marking knife to make clear and accurate lines. Pencils are great for marking general outlines, while marking knives provide precise lines that are easy to follow.
- Ruler Method: To mark parallel lines, place a ruler on the wood and run your marking tool along the edge. This technique ensures consistency and prevents the need for measuring multiple times.
- Story Stick: A story stick is a handy tool for replicating measurements and dimensions. It is essentially a thin strip of wood with markings that represent specific measurements. Use a story stick to transfer measurements from one piece to another easily.
Layout and Planning
Before diving into your woodworking project, take the time to plan and lay out your design. This step will help you visualize the end result and ensure that all components fit together perfectly. Here are some layout and planning techniques:
- Blueprints: Create a detailed blueprint or sketch of your project. This will serve as a roadmap and help you make accurate measurements, identify potential challenges, and plan your cuts and joinery.
- Mock-Ups: Consider creating a mock-up or prototype of your project using inexpensive materials. This will allow you to test your design, make adjustments, and ensure that everything fits together correctly.
- Marking Gauges: A marking gauge is a useful tool for marking consistent lines at a specific distance from the edge of your wood. This is particularly helpful for tasks such as marking mortises and tenons.
Remember, the key to accuracy in woodworking is to measure twice and cut once. Take your time with measuring and marking, and always double-check your measurements before making any cuts or joints. By mastering these techniques, you'll be well on your way to maximizing efficiency and precision in your woodworking projects.
Continue reading: Cutting and Shaping Methods
Cutting and Shaping Methods
When it comes to woodworking, cutting and shaping is an essential part of the process. Whether you're a beginner or an experienced woodworker, using the right tools and techniques can make a significant difference in the precision and efficiency of your projects. In this section, we'll explore some effective cutting and shaping methods that will help you achieve the best results in your woodworking endeavors.
Using Hand Tools Effectively
Hand tools are an integral part of any woodworker's arsenal. While power tools offer speed and convenience, there's something satisfying about using hand tools for fine woodworking tasks. Here are a few tips to help you use hand tools effectively:
- Sharp Tools - Keep your hand tools sharp by regularly honing and sharpening them. Dull tools not only make the task more difficult but can also lead to accidents.
- Proper Technique - Learn and practice proper hand tool techniques, such as how to grip the tool correctly and control your strokes. This will improve the quality and accuracy of your cuts.
- Practice Patience - Take your time when using hand tools. Rushing can lead to mistakes and compromised results. Remember, woodworking is as much about the process as it is about the end result.
Power Tools for Precise Cuts
Power tools are designed to provide efficiency and accuracy in cutting and shaping wood. Here are a few power tools commonly used in woodworking:
- Circular Saw - A circular saw is versatile and can be used for various cutting tasks. Make sure to adjust the depth and angle of the blade to achieve precise cuts.
- Jigsaw - A jigsaw is perfect for cutting curves and irregular shapes. It's a must-have tool for projects that involve intricate designs.
- Router - Routers are ideal for creating decorative edges, joinery, and even intricate carvings. With the right bit, you can achieve professional-looking results.
- Table Saw - A table saw is a powerful tool that offers accurate and straight cuts. However, it requires proper setup and safety precautions for optimal usage.
Remember, power tools can be dangerous if not used correctly, so always prioritize safety. Familiarize yourself with the manufacturer's instructions and wear appropriate safety gear, such as safety glasses and gloves.
Creating Complex Shapes and Joints
Woodworking often involves creating complex shapes and joints. Here are a few techniques that can help you achieve these intricate designs:
- Scroll Saw - A scroll saw is perfect for cutting delicate and intricate patterns. It allows for precise control and maneuverability, making it an excellent tool for decorative detailing.
- Chisels and Gouges - Chisels and gouges are essential for shaping wood and creating intricate details. They come in various sizes and shapes to accommodate different types of cuts.
- Dovetail and Mortise-and-Tenon Joints - These traditional joinery techniques are commonly used for their strength and visual appeal. They require precision and skill but result in robust connections.
- Band Saw - A band saw is versatile and can handle both curves and straight cuts. It's an excellent tool for creating irregular shapes and cutting thick stock.
By utilizing these cutting and shaping methods, you'll be able to take your woodworking projects to the next level. Combine these techniques with proper planning and measurement, and your creations will exude professionalism and finesse.
"Using the right cutting and shaping methods in woodworking is like adding the perfect strokes to a piece of art. It's all about precision and finesse."
Joinery Techniques for Strength and Durability
When it comes to woodworking, joinery techniques play a crucial role in ensuring the strength and durability of your projects. Joinery refers to the act of connecting two or more pieces of wood together to form a secure and stable bond. Whether you're building cabinets, furniture, or anything else, using the right joinery method can make all the difference in the longevity and structural integrity of your creations.
Different Joinery Methods
There are numerous joinery methods to choose from, each with its own advantages and best use cases. Here are some common joinery techniques to consider:
- Dovetail Joints: Dovetail joints are known for their strength and durability. They are widely used in furniture making, particularly for drawers. The interlocking shape of dovetail joints prevents the pieces from pulling apart, creating a strong bond that can withstand the test of time.
- Mortise and Tenon Joints: Mortise and tenon joints are versatile and commonly used in woodworking. This joint involves cutting a square or rectangular hole (mortise) into one piece of wood and inserting a corresponding projecting piece (tenon) from the other piece. Mortise and tenon joints provide a strong connection and are often used for constructing frames and tables.
- Box Joints: Box joints, also known as finger joints, are created by interlocking rectangular cuts in two adjoining pieces of wood. This type of joint offers both strength and visual appeal. Box joints are commonly used in box construction and drawer assembly.
- Dowels: Dowels are cylindrical wooden pins used to join two or more pieces of wood together. The dowel holes are drilled into the wood, and then the dowels are inserted and glued into place. Dowels provide a reliable and sturdy connection, especially when used in conjunction with other joinery methods.
Choosing the Right Fasteners
In addition to using joinery techniques, it's essential to select the right fasteners to further reinforce your woodworking projects. Fasteners, such as screws, nails, and bolts, can help add strength and stability to the joints. Consider the following when choosing fasteners for your project:
- Screws: Screws are versatile and come in various sizes and types. They provide excellent holding power and are ideal for joining pieces of wood together. For added strength, consider using screws with threaded shanks or coated screws designed specifically for woodworking.
- Nails: Nails are commonly used in woodworking projects and offer a quick and straightforward way to connect wood pieces. However, they may not provide as much strength as other fasteners, so they are often used in conjunction with other joinery methods.
- Bolts: Bolts are threaded fasteners that require pre-drilled holes for installation. They provide a secure connection that can be tightened or loosened as needed. Bolts are often used in structural applications where extra strength is required.
Gluing and Clamping Tips
In addition to mechanical fasteners, glue can be an effective way to strengthen and reinforce your joinery. When using glue, consider the following tips:
- Choose the right glue: Different glues have different properties and drying times. Choose a woodworking glue that is suitable for your specific application. Wood glues such as PVA (Polyvinyl Acetate) and Polyurethane-based glues are commonly used in woodworking projects.
- Apply even pressure: When applying glue, make sure to distribute it evenly across the surfaces to be joined. Use a brush or a spatula to spread the glue evenly and ensure adequate coverage.
- Clamp for optimal bonding: Applying clamping pressure helps to ensure a strong bond between the joined pieces. Use clamps to hold the pieces together firmly while the glue dries. Clamp placement and pressure are crucial, so follow the manufacturer's instructions for the specific type of glue you are using.
By selecting the right joinery method, choosing appropriate fasteners, and properly using glue and clamping techniques, you can create woodworking projects that are not only aesthetically pleasing but also robust and long-lasting. Remember, practice and experimentation are key to mastering joinery techniques, so don't be afraid to try different methods and learn from your experiences. Happy woodworking!
Finishing and Sanding Tips
When it comes to woodworking projects, the finishing and sanding process can make all the difference in the final result. A smooth, polished finish not only enhances the overall appearance of your work but also protects the wood from damage and wear. In this section, we will explore some valuable tips for achieving a professional finish and sanding your projects with precision.
Preparing the Surface
Before you start applying any finish, it is crucial to properly prepare the surface of your woodworking project. Here are a few steps to follow:
- Sanding: Begin by sanding the wood to smooth out any imperfections, such as rough patches or splinters. Start with a coarse-grit sandpaper and gradually work your way up to a finer grit for a smoother finish.
- Filling: If there are any noticeable gaps, holes, or cracks in the wood, use wood filler to fill them in. Allow the filler to dry completely before sanding it down to achieve a seamless surface.
- Cleaning: Make sure the wood surface is free from dust and debris before applying any finish. Use a damp cloth or a vacuum with a brush attachment to remove any particles.
Choosing the Right Finishes
The type of finish you choose depends on the desired look and level of protection you want for your woodworking project. Here are a few popular finish options:
- Stain: Stains are used to add color to the wood while allowing the natural grain to show through. They come in a variety of shades and can be oil-based or water-based.
- Varnish: Varnishes provide a protective layer over the wood, enhancing its durability. They can be glossy, semi-gloss, or matte, depending on the desired sheen.
- Paint: If you prefer a solid color or want to add a touch of creativity to your project, paint can be a great choice. It provides a durable finish and allows for endless color options.
When selecting a finish, consider factors such as the type of wood you are working with, the project's intended use, and the level of maintenance you are willing to commit to.
Sanding Techniques for a Smooth Finish
Sanding is a crucial step in achieving a smooth and polished surface. Here are a few tips to keep in mind:
- Start with a lower grit: Begin with a lower grit sandpaper for initial sanding to remove any roughness or imperfections on the wood surface.
- Move to higher grits: Gradually increase the grit size to achieve a finer finish. This will help to smooth out the scratches left by the previous coarse-grit sandpaper.
- Sand in the direction of the wood grain: Always sand in the direction of the wood grain to avoid creating visible scratches that may be difficult to remove later.
- Check for smoothness: After each sanding pass, run your hand across the wood to feel for any rough patches. If you encounter roughness, continue sanding until the surface feels smooth to the touch.
- Use sanding blocks: Sanding blocks can help distribute pressure evenly across the wood surface, preventing uneven sanding or dips in the wood.
Remember to be patient and take your time during the sanding process. Rushing can lead to uneven results and compromise the overall finish quality of your woodworking project.
By following these finishing and sanding tips, you can achieve a professional and polished look for your woodworking projects. A well-executed finish not only enhances the beauty of the wood but also protects it from daily wear and tear, ensuring its longevity. So, take your time, choose the right finishes, and employ proper sanding techniques to create woodworking masterpieces that will impress for years to come.
Ensuring Safety and Cleanliness
When it comes to woodworking, ensuring safety and cleanliness should be a top priority. Woodworking involves using sharp tools and working with potentially harmful materials, so taking the necessary precautions is essential. In this section, we will discuss various measures you can take to keep yourself and your workspace safe and clean.
Proper Personal Protective Equipment (PPE)
Wearing the right personal protective equipment (PPE) is crucial when working with wood. Here are some essential items to consider:
- Safety glasses: Protect your eyes from flying wood chips and debris.
- Ear protection: Invest in earplugs or earmuffs to shield your ears from the loud machinery.
- Dust mask or respirator: Keep harmful dust particles out of your lungs.
- Gloves: Choose gloves that provide both dexterity and protection, especially when handling sharp tools.
- Apron or smock: Keep your clothing clean and protected from splinters and stains.
Dust Collection and Woodshop Ventilation
Woodworking produces a significant amount of dust, which can be harmful if inhaled. Effective dust collection and proper ventilation are essential for a safe and clean woodworking environment. Here's what you need to know:
- Dust collection system: Invest in a quality dust collector or a shop vacuum with a dust collection attachment to remove as much dust as possible while you work.
- Air filtration system: Consider using an air filtration system to continuously purify the air in your workshop, reducing the risk of respiratory issues.
- Open windows and fans: Increase air circulation by opening windows and using fans to prevent dust buildup and maintain a comfortable working environment.
- Cleaning routine: Develop a regular cleaning routine to sweep and vacuum your workshop to keep it free of dust, wood shavings, and debris.
Safe Handling of Tools and Materials
Proper tool handling is crucial to avoid accidents and injuries. Follow these tips to ensure safe woodworking practices:
- Sharp tools: Keep your cutting tools sharp to reduce the risk of slips and accidents. Dull tools can be more dangerous as they require more force to use.
- Proper tool storage: Organize your tools in a way that minimizes the risk of accidents. Use designated tool racks, cabinets, or drawers to keep them safely stored when not in use.
- Secure workpieces: Avoid the risk of your workpiece slipping or moving during a cutting or shaping operation by securely clamping it in place.
- Chemical storage: If you use finishes, glues, or other chemicals in your projects, store them in a designated area away from heat sources and out of reach of children and pets.
- Proper disposal: Dispose of waste materials, such as sawdust, wood scraps, and chemical containers, responsibly and according to local regulations.
Remember, safety should always be a priority in your woodworking endeavors. By following these safety measures and maintaining cleanliness in your workshop, you can enjoy your woodworking projects with peace of mind.
"Safety first is safety always." - Charles M. Hayes
Troubleshooting and Problem Solving
Woodworking projects don't always go as planned. Even the most experienced woodworkers encounter issues and challenges along the way. But fear not! With the right troubleshooting techniques and problem-solving skills, you can overcome any obstacle that comes your way. Here are some tips to help you troubleshoot and solve common woodworking problems:
Identifying and Fixing Common Woodworking Issues
- Issue: Uneven or Rough Surfaces
Solution: Use a hand plane or sandpaper to level the surface. Start with a coarse grit sandpaper and gradually work your way to a finer grit for a smoother finish. - Issue: Splitting or Splintering Wood
Solution: Prevent splitting by pre-drilling holes for screws or nails. When cutting wood, make sure your saw blade is sharp and use a backing board to prevent tear-out. - Issue: Misaligned Joints
Solution: Check for squareness and adjust as necessary. Use clamps to hold the pieces in place while the glue dries. If the joint is still misaligned, you may need to disassemble and start again.
Dealing with Warping and Moisture Problems
- Issue: Wood Warping or Bowing
Solution: To prevent warping, store wood in a climate-controlled environment with consistent humidity levels. If wood has already warped, try steam bending or using weights to straighten it. - Issue: Moisture-related Problems
Solution: Ensure that you are working with properly dried wood. Use a moisture meter to check the moisture content. If you notice dampness or mold, remove the affected areas and allow the wood to dry before proceeding.
Repairing Mistakes
- Issue: Accidental Chipping or Scratches
Solution: If the damage is minor, you can use wood fillers to fill in the chipped or scratched area. Sand and refinish to match the surrounding wood. For deeper gouges, consider replacing the damaged piece. - Issue: Glue Squeeze-out
Solution: Allow the glue to partially dry and then scrape off the excess with a chisel or putty knife. If the glue has hardened, use a special adhesive remover or carefully sand away the excess.
Remember, problem-solving in woodworking requires patience and creativity. Don't get discouraged when faced with challenges; instead, view them as opportunities to learn and grow as a woodworker. By honing your troubleshooting skills, you'll become more confident in tackling any issue that arises during your projects.
"The measure of success is not whether you have a tough problem to deal with, but whether it is the same problem you had last year." - John Foster Dulles
Taking Your Woodworking Skills to the Next Level
Congratulations on mastering the fundamentals of woodworking! Now that you have a strong foundation, it's time to take your woodworking skills to the next level. Whether you want to explore more advanced techniques, tackle complex projects, or connect with other woodworking enthusiasts, there are plenty of ways to continue growing as a woodworker. Let's dive in!
Continued Learning and Skill Development
Woodworking is an art that requires ongoing learning and skill development. By continually expanding your knowledge and honing your techniques, you can become a more proficient woodworker and take on increasingly challenging projects. Here are a few ways you can continue your woodworking education:
- Online Resources: The internet is a treasure trove of woodworking tutorials, videos, forums, and blogs. Take advantage of these free resources to learn new techniques, discover innovative ideas, and gain inspiration from other woodworkers.
- Courses and Workshops: Consider enrolling in woodworking courses or workshops offered by local community colleges, vocational schools, or woodworking studios. These hands-on experiences provide valuable guidance from experienced instructors and allow you to learn new skills in a structured environment.
- Books and Magazines: Explore woodworking literature to deepen your understanding of different techniques, design principles, and project ideas. Look for books written by seasoned woodworkers or subscribe to woodworking magazines for regular doses of inspiration and knowledge.
Exploring Advanced Techniques and Projects
Once you have a strong grasp of the basics, it's time to challenge yourself with more advanced techniques and projects. Here are a few areas you can explore to expand your woodworking repertoire:
- Fine Furniture Making: Delve into the world of fine furniture making, where precision joinery techniques and meticulous attention to detail are paramount. Create heirloom pieces that showcase your craftsmanship and artistic flair.
- Cabinetmaking: Expand your skills by diving into cabinetmaking. Learn to create beautiful and functional cabinets, wardrobes, and storage solutions. Master the art of fitting doors, installing hardware, and creating custom interiors.
- Woodturning: Explore the art of woodturning, where cylindrical pieces of wood are transformed into intricate shapes. With a lathe and some turning tools, you can create beautiful bowls, vases, pens, and decorative objects.
- Marquetry and Inlay: Add a touch of elegance to your woodworking projects by incorporating marquetry and inlay techniques. Learn how to create intricate patterns and designs by integrating different types of wood, veneers, and other materials.
Participating in Woodworking Communities
Connecting with other woodworkers is a fantastic way to learn, share ideas, and get inspiration. Joining woodworking communities allows you to interact with like-minded individuals who share your passion for the craft. Here are some ways you can participate in woodworking communities:
- Woodworking Clubs: Join local woodworking clubs or associations where you can attend meetings, workshops, and events. These clubs often have seasoned woodworkers who are more than willing to share their knowledge and mentor beginners.
- Online Forums: Engage in online woodworking forums where you can ask questions, seek advice, and share your projects with a supportive community. These platforms provide an excellent opportunity to learn from experienced woodworkers and connect with enthusiasts from around the world.
- Woodworking Expos and Shows: Attend woodworking expos and shows to see the work of master craftsmen, discover new tools and techniques, and connect with vendors and professionals in the industry. These events are not only educational but can also serve as a source of inspiration for future projects.
By immersing yourself in woodworking communities, you can gain valuable insights, learn from the experiences of others, and forge meaningful connections with fellow woodworkers.
As you embark on your woodworking journey, remember that mistakes are a part of the learning process. Embrace the challenges, seek out new knowledge, and continue to push the boundaries of your skills. With time and dedication, you'll become an accomplished woodworker capable of creating stunning pieces that showcase your passion and talent.
Now go forth and unleash your creativity in the world of woodworking! Happy woodworking!
Conclusion
In conclusion, maximizing efficiency and precision in your woodworking projects is key to producing high-quality pieces that you can be proud of. By setting up a well-equipped workshop, selecting the right wood, using accurate measuring and marking techniques, employing effective cutting and shaping methods, utilizing strong joinery techniques, implementing proper finishing and sanding techniques, prioritizing safety and cleanliness, troubleshooting and problem-solving, and continually improving your skills, you can take your woodworking to the next level.
Woodworking is a fulfilling and rewarding hobby or profession that allows you to create functional and beautiful pieces. By following the tips and techniques outlined in this article, you can ensure that your projects are not only visually appealing but also durable and long-lasting. Remember to always prioritize safety and cleanliness in your workshop to protect yourself and prolong the lifespan of your tools.
It's important to approach woodworking with a growth mindset, continually seeking out opportunities to learn and improve your skills. Whether it's through online tutorials, workshops, or engaging with woodworking communities, th
Frequently Asked Questions
- What are some woodworking tools that can help maximize efficiency?Some woodworking tools that can help maximize efficiency include a table saw, miter saw, router, and power drill. These tools enable precise cuts, shaping, and joining of wood, reducing time and effort required for each project.
- How can I ensure precision in my woodworking projects?To ensure precision in woodworking projects, use high-quality measuring tools like a tape measure, combination square, and calipers. Additionally, invest in sharp and properly adjusted cutting tools, secure workpieces firmly, and double-check measurements before making cuts.
- What are some techniques for improving efficiency in woodworking?Some techniques for improving efficiency in woodworking include organizing your workspace, planning projects in advance, using templates and jigs for repetitive tasks, and optimizing material usage to minimize waste.
- How can I improve accuracy when making joinery in woodworking?To improve accuracy in woodworking joinery, use precise marking and measuring techniques, make test cuts or trial assemblies, use clamps or fixtures to secure workpieces during assembly, and regularly maintain and sharpen cutting tools for clean and precise cuts.
- Are there any software programs available for woodworking project planning and design?Yes, there are several software programs available for woodworking project planning and design. Some popular options include SketchUp, AutoCAD, and Fusion 360. These programs allow you to create detailed plans, visualize your projects in 3D, and accurately estimate material requirements.